CoCoNut Work Packages
Work Packages
WP1 - management
WP2 - Requirements Synthesis and Core Concept Generation
- Market survey carried out to identify commercially available 'trapped tooling' options for production of hollow aircraft composite part
- Selection criteria defined. General characteristics of the dry fibre, resin material, and process requirements (7 Bars RTM injection pressure, 180°C curing temperature) agreed upon.
- Among the candidate 'trapped tooling' internal core materials investigated in the market survey, a suitable material conforming to the selection criteria was identified. "Cavuscore", a castable water-soluble mandrel composed of bauxite or glass beads matrix with polymer binder was selected, in particular due to its resistance to high injection pressures.
- Various options for sealing the water-soluble mandrel, to best prevent resin infiltration during RTM investigated.
- Integrated internal heating concepts identified to help ensure complete curing of thicker sections of the CFRP part
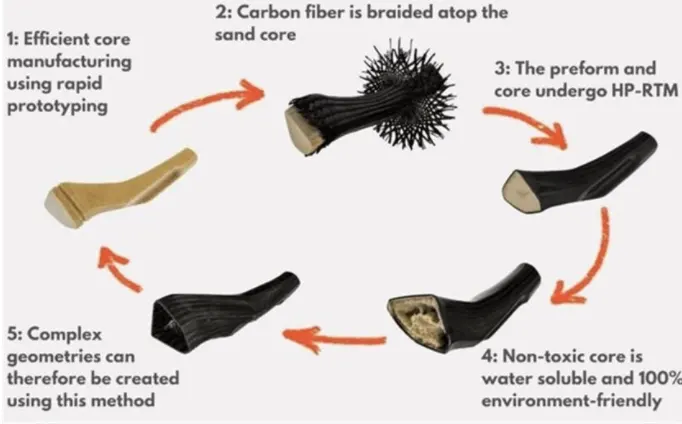
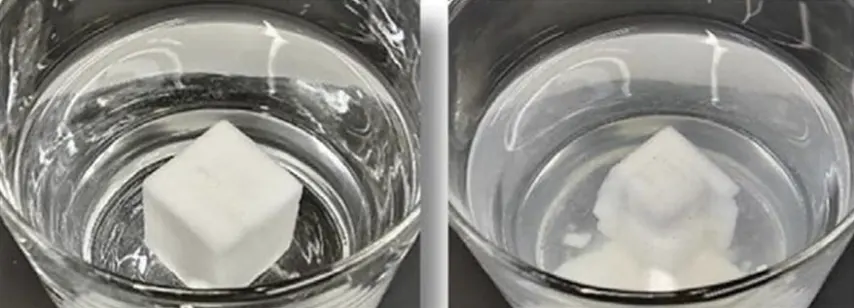
Example of "Cavuscore" process, and dissoluton of "Cavuscore" mandrel in water
WP3 - Design of demonstrator part, complex cores, and RTM tool
- A CFRP demonstrator part to be manufactured by RTM was designed, based on the geometry of a cross beam landing gear part, with internal cavity, complex geometry, and a variable wall thickness of 6-20 mm.
- A hybrid internal mandrel was designed, consisting of a water-soluble "Cavuscore" mandrel mounted on an internal metal shaft, to create the hollow internal geometry of the demonstrator part.
- Polymer heatshrink tube was selected as the material of choice for sealing the water-soluble mandrel.
- Included in the design are metallic end rings, to be removed after curing to allow water access to the water-soluble mandrel
- An RTM tool was designed and manufactured to meet the part design and process requirements.
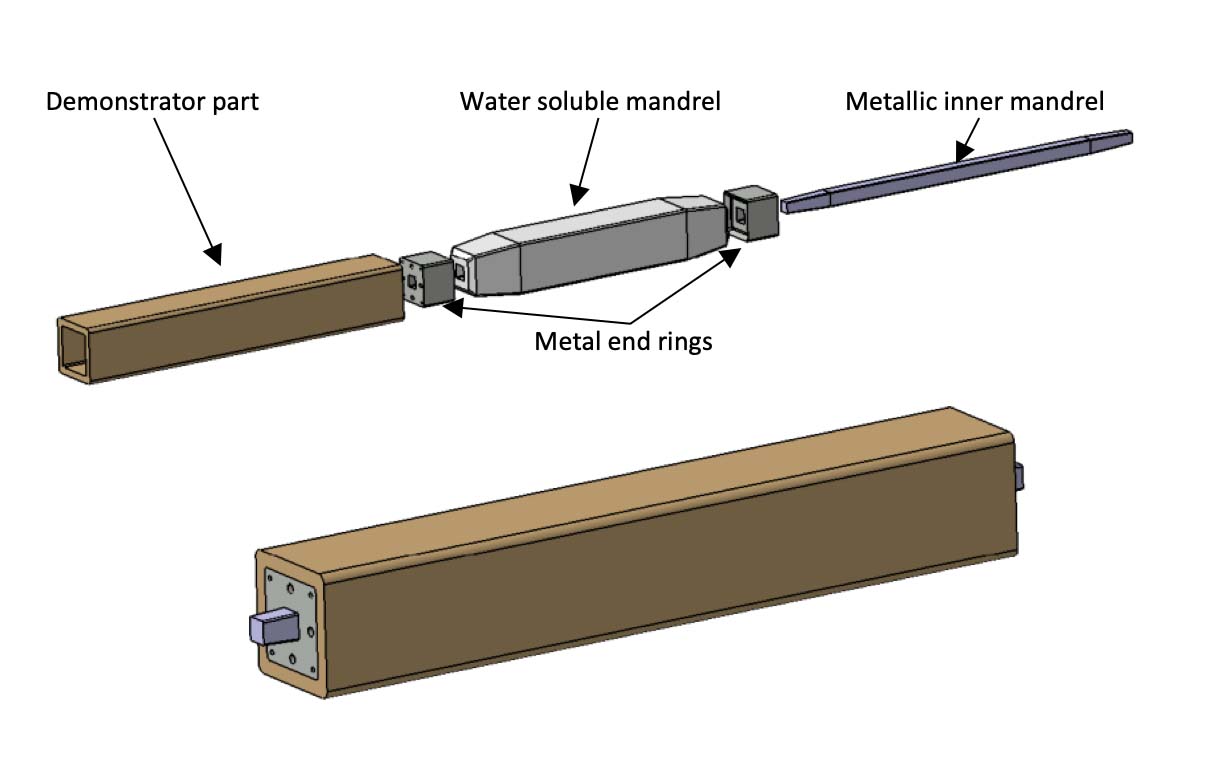
Design of demonstrator part & complex cores
WP4 - RTM core manufacturing, tool procurement, and preform manufacturing
- • Production of metal mandrels and casting of water-soluble mandrel for producing hollow demonstrator part's complex internal geometry
- Production of RTM tool
- Production of test parts, followed by QA testing
- Final adjustments to RTM tool
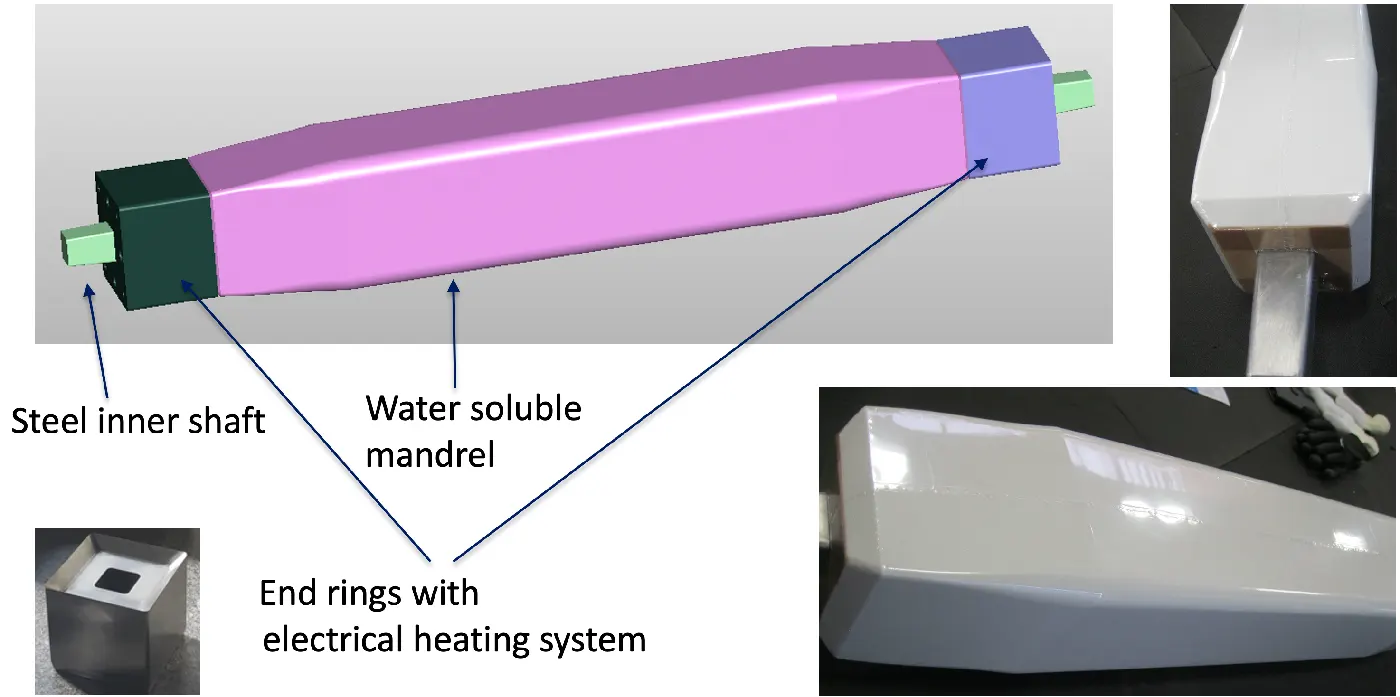
WP5 - RTM core test and demonstration
- Production of Proof of Concept parts, with and without the application of localised internal heating, plus final demonstrator part
- QA testing
WP6 - Test and demonstration reporting
- Documentation of final results, analysis, and conclusions